THE OBTECT
WHY
THE OBTECT
DEVELOPED
Many hazardous chemicals are used in semiconductor and display manufacturing processes, and countless pipelines are used to supply chemicals to various manufacturing equipment.
The inside of these pipes can be corroded by harmful chemicals, and the most vulnerable place is the "pipe connection part" that changes the
direction or lengthens the pipe.
To this connection, an O-ring made of chemical-resistant rubber is applied to minimize the gap in the joint, and this O-ring is the first to be gradually damaged, leading to a leak accident. Although these leaks are not frequent, they do occur unexpectedly, and there is a problem that can lead to not only huge property damage due to the interruption of the manufacturing process, but also human accidents. Therefore, to prevent this, a system that can detect minute leaks of hazardous chemicals in advance and notify the manager is required.
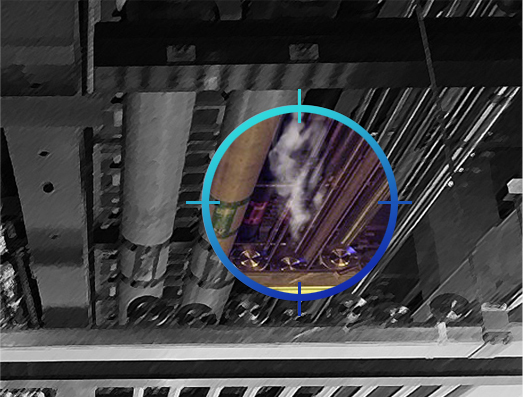
MICROVIBRATING
MICROSEISM
vibration, pulsation,corrosion, and hardening
-
Toxic gases and chemicals gradually corrode the sealing of the pipe connection part and the O-ring inside the clamp, weakening the durability in the hardened state, and leaking after cracks occur.
-
Leakage of poisonous flammable gas and chemicals occurs after micro-distortion of the pipe joint due to vibration and pulsation inside the pipe
-
Huge
cost loss -
Human
casualties -
decline in corporate
reputation
EXISTING
USING CLAMP
To solve this problem,
a clamp is installed on the pipe connection part.
The clamp prevents loosing of pipe joint,
avoiding gas and chemical leaks
However, poisonous and flammable
gas/chemical cannot even seal
the pipe joint and block the O-ring
inside the clamp.
The fine gap between the clamp and O-ring
causes gas/chemical leaks due to vibration,
pulsation, and chemical reaction.
-
Before Gas/Chemical leaks
-
After Gas/Chemical leaks
Most of the clamp products are certified by various organizations and distributed on the market, but the certification standards are not keeping up with the pace of development of the high-tech industry.
LIMITS OF
CLAMP IN MARKET.
we need the right product
-
Endurance limit
The sealing of the pipe joint and even the internal O-ring cannot be blocked
-
Actions after damage
Gas/chemical leak signal must occur over a certain range
-
Difficulty removing leaks
As harmful gas/chemicals has already spread around the pipe joint, It is difficult to remove
-
Arbitrary release problem
There is a risk of accidents because the device can be released arbitrarily
OBTECT OVERVIEW.
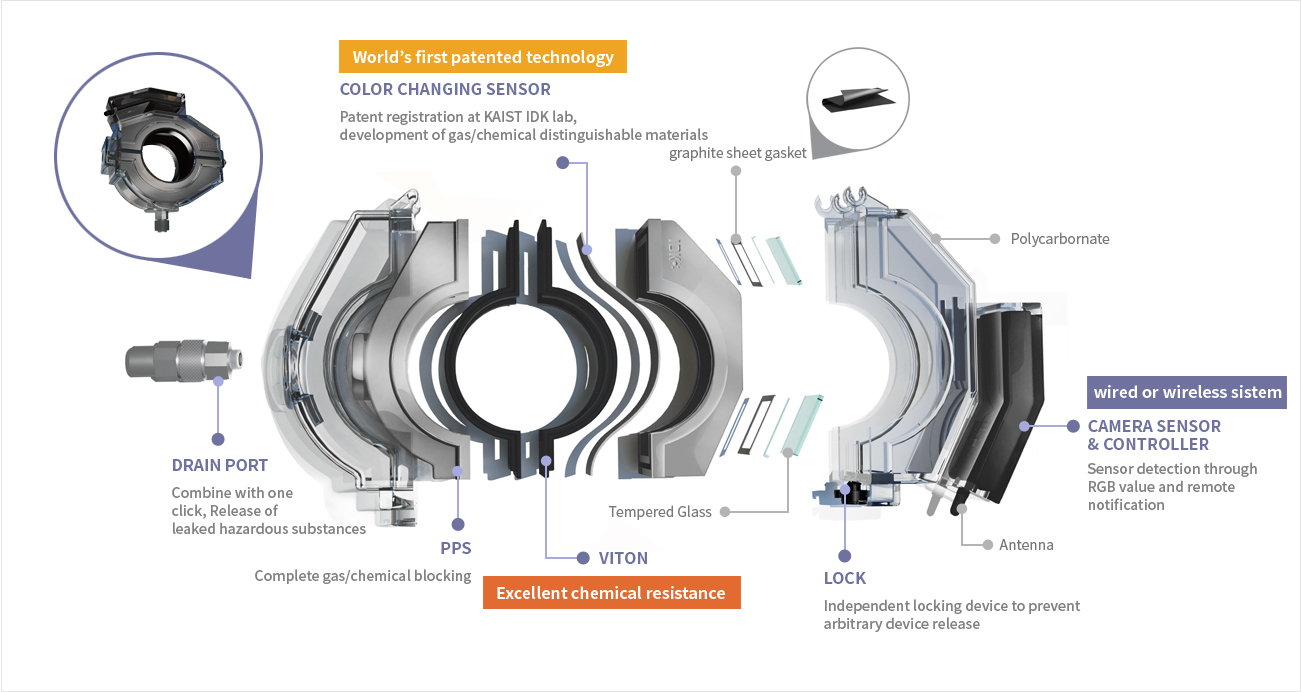
COLOR CHANGING
SENSOR.
CAMERA SENSING.
CABLE OR BATTERY.
HIGH DURABILITY
OF VITON & PPS.
720
hours more than
Leak containment of gas and
chemical as hazardous substances
DRAIN PORT.
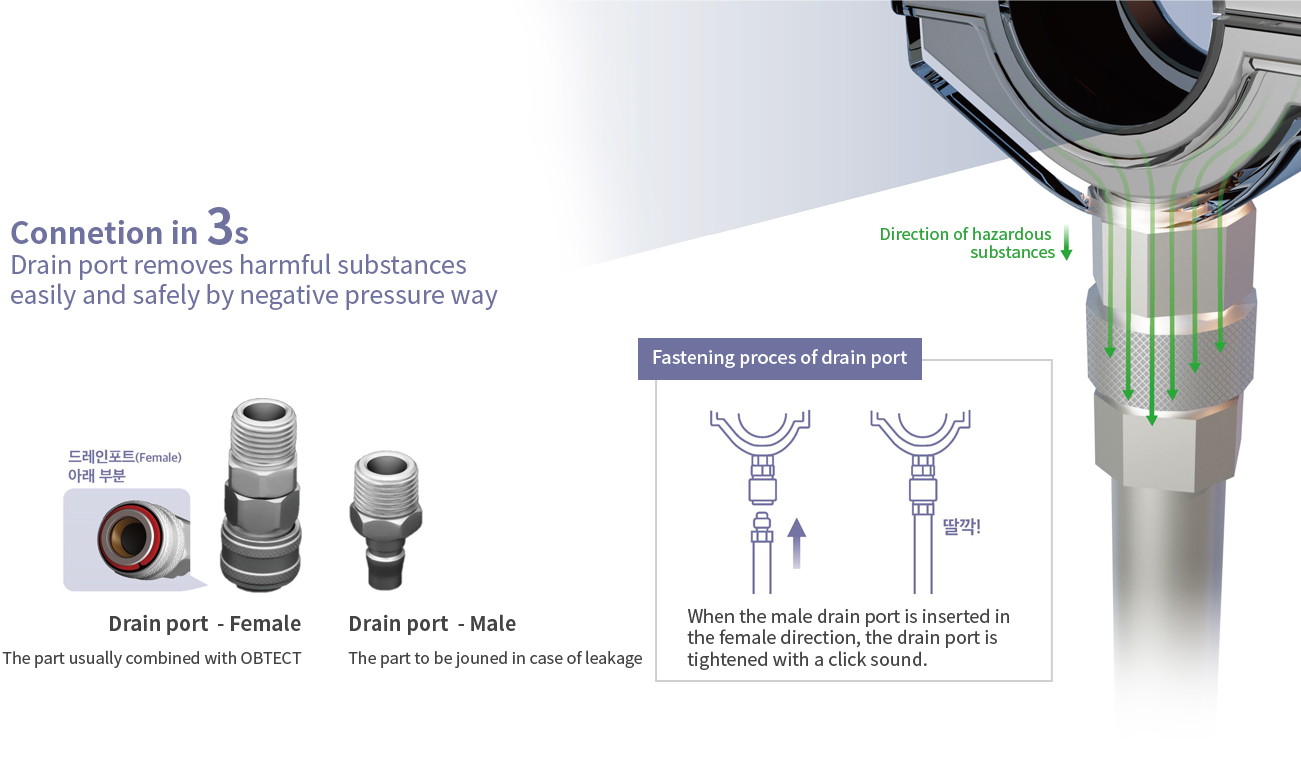
LOCK
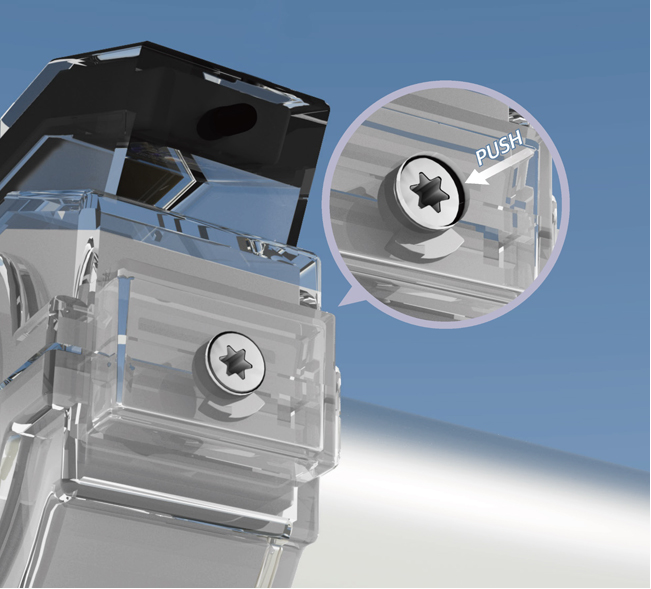
arbitrarily by anyone other than the
authorized person
Prevent the spread of damage and maintain safety
and confidentiality
A locking device made using proprietary technology prevents
damage from spreading due to leaks, protects users,
and maintains confidentiality.
-
01Push after combining
the dedicated key -
02Rotate clockwise
-
03Top polycarbonate case open
SENSING PROCESS.
The OBTECT controls the leak situation with the
control equipment as follows.
Through this, unlike in the past, it is possible to
clearly identify and control the leak situation.
leak status, notification of leak
occurrence and location confirmation
color change sensor to removal
of harmful substances through
the drain port
-
01Change of colorimetric sensor
and operation of optical sensorWith gas/ chemical leaks Color of the sensor progress
-
02Signal transmission
to control equipment after optical
sensor reaction -
03Understanding the situation with control equipment By identifying the signal transmitted from the sensor, it notifies that a leak has occurred and iden- tifies the location of the leak. (P&ID applied)
-
04With tempered glass, check for actual leaks
Visually observe the color variation to check for leaks once more
-
05Gas/chemical emissions through drain port
Poisonous and flammable gas/chemical in the leaking pipe connection part are removed safely through the drain port
CONTROL
EQUIPMENT.
-
Intuitive UX/UI OBTECT
control unit check the
status of OBTECT and the
pipe connection part.
UX/UI configuration for easy
understanding,
OBTECT notification that a leak
occurred by detecting the signal of OBTECT -
1,000:1
1,000 OBTECTs with
one control device -
COLOR SENSOR
- · No product could ever before
- · High-speed, high-sensitivity response
- · 3D porous nanofiber technology
NO PRODUCT
COULD DO
EVER BEFORE.
-
Real-time development of
toxic gas/chemical detection
color sensor materials -
Technology innovation of
color sensor Toxic gas
detection library is presented
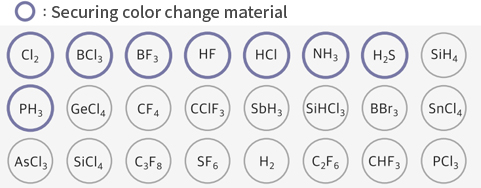
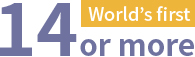
Gas/Chemical classification
possible
Real-time detection as
well as safe discharge of
hazardous substances
Manufacturing company |
GIF KOREA | American Gas & Chemical |
ROCOL (Part of ITW) |
Nitto |
![]() |
---|---|---|---|---|---|
Country | South korea | U.S.A | U.K | Japan | South korea |
Detection method |
PH responsive Taping method |
Gas detectable dye responsive |
Spray method | Gas detectable dye responsive |
Nanofiber based Gas detectable dye responsive Direct connection to the pipe or joint |
Sensing material |
Acid and base (liquid) | Cl₂, NH₃, H₂S, CO | Cl₂, NH₃, H₂S, CO | NH₃, H₂ |
14 or Gas, Chemical |
Performance and feature |
Detection limit Reaction time Suitable for liquid phase reactions but limited gas detection |
Detection limit Reaction time Expensive |
Detection limit Reaction time No real-time detection |
Detection limit Reaction time |
Sensitive detection |
Product image |
![]() |
![]() |
![]() |
![]() |
![]() |
FAST CHANGING,
SENSITIVE REACTION
-
Before color change
-
After color change
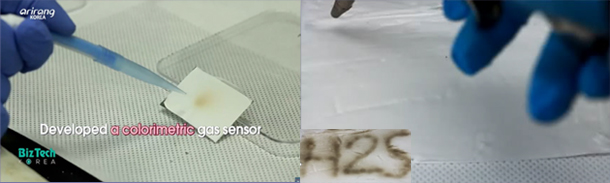
3D POROUS NANOFIBER
TECHNOLOGY - PATENTED.
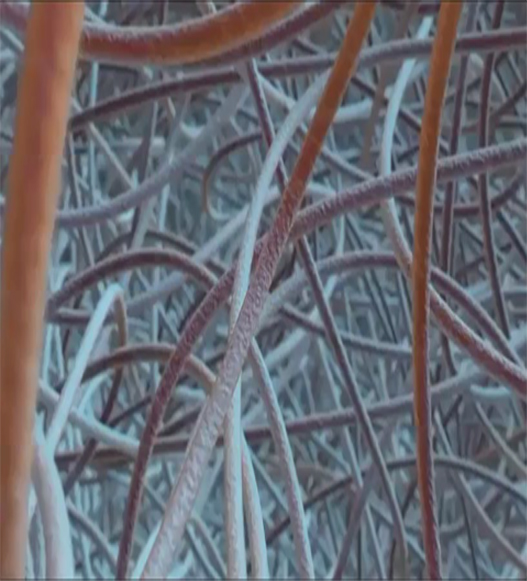
-
Completion of production facility nanofiber
alignment electrospinning machineEstablishment of facilities for mass production
of 3D porous nanofiber color change sensor -
1/10of a spider's web
0.3μm(micrometer)
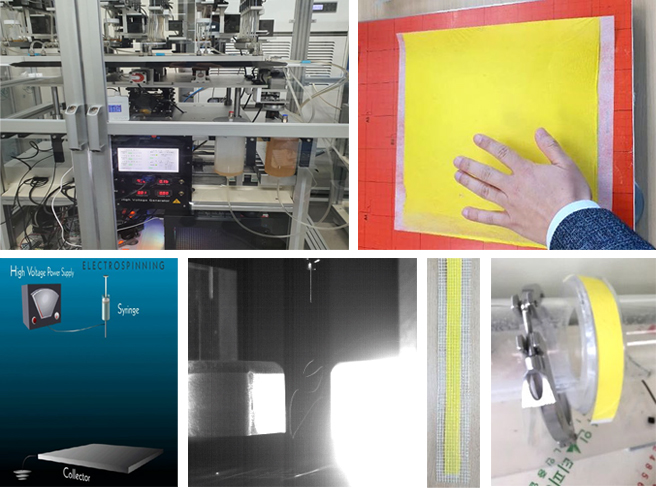
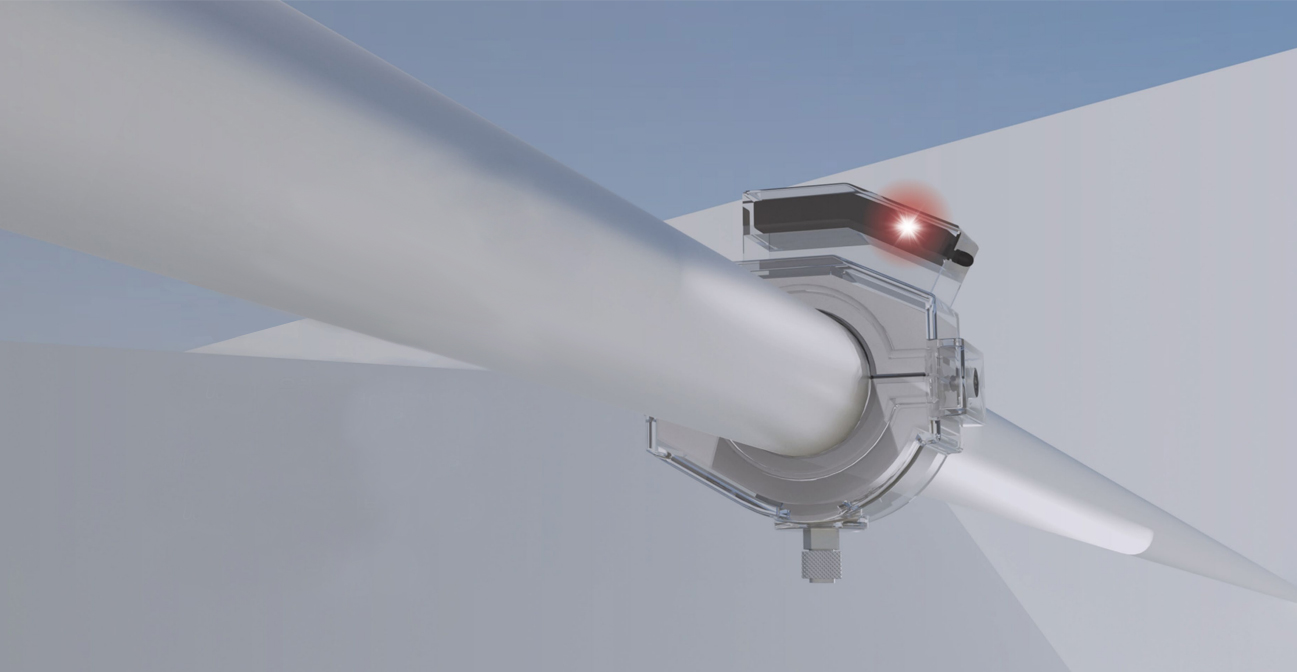
Complete prevention
and control of leaks.
-
01
Can be installed without linestop
-
02
Real-time LEAK monitoring
-
03
Blocking external leakage
-
04
No need to report leaks
APPENDIX.
Proof of product excellence through test reports
-
PPS chemical resistance test NNFC
-
OOBTECT performance test NNFC
-
Camera module performance test